Med internationellt ledande teknologi vill vi skapa tillväxt på hemmaplan.
Två maskinverktyg kopplade med full autonomi
Automatiserad magnesiumbearbetning med hög pålitlighet
Magnesium is the lightweight metal with the lowest density: about one quarter of the density of steel and 35% less than aluminium. Anyone caring to consult the technical literature will learn that low cutting forces are required for machining, resulting in reduced tool wear. In the context of automation of a machining process, this means rigid requirements in terms of the reliability and technical availability of automation and workpiece autonomy.
Put in a nutshell: the system must operate smoothly and reliably for long periods, and offer a sizeable workpiece buffer for raw and finished parts that can be replenished and emptied at any time, while providing adequate capacity to operate at night or over a weekend without operator intervention.
In the specific case, the machining of the two faces of the workpiece takes place consecutively on two machines, fourfold on the first machining centre and singly on the second machine. In the course of machining, the area should be accessible for manual setup processes. The additional marking of workpieces with a data matrix code after machining should be integrated into the automation process.
Schwab CNC Metallbearbeitung has been producing high-quality milled and turned parts for a variety of industries since 2010. In line with the company philosophy “Professional support over the entire product life-cycle – from prototype development and series production to the spare part”, single prototypes and larger series are produced by aluminium and magnesium pressure die casting.
The performance spectrum of the company, whose head office is at Rot am See (District of Schwäbisch Hall) in the Franconian north-east of Baden-Württemberg, also includes in-depth technical consultation of the customer prior to and during a project. The family-owned enterprise with 14 employees is managed by father Reiner and son Markus Schwab.
The automation was developed and implemented as a turnkey system by EGS Automatisierungstechnik GmbH from Donaueschingen in the Schwarzwald-Baar district. The company has been actively involved in the field of industrial automation since 1996, and has employed industrial robots for the purpose since 1999. Its customers benefit from the company’s expertise: over 1,750 robots had been installed by the time the described system was started up in 2019.
The ‘actuator housing’ workpiece is a magnesium housing component for the steering gear of motor vehicles that Schwab has been producing for some time. The main impetus for automating the machining of parts resulted from a substantial increase in demand, requiring an annual production of up to 250,000 parts. Because it also has to contend with a shortage of skilled workers, this move enabled the company to release many employees who were hitherto manually involved in the process for other activities where they were urgently needed.
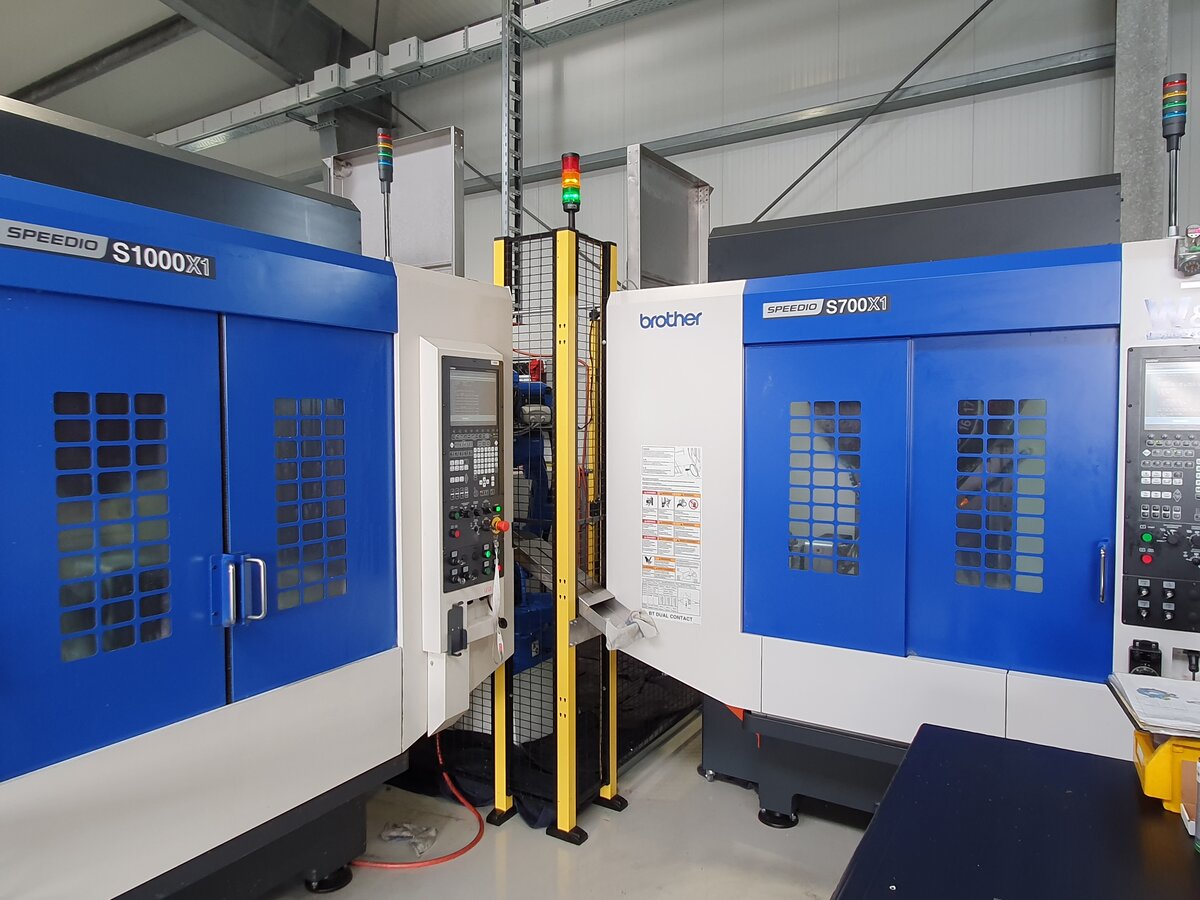
The starting point for the automation process was an existing Brother Speedio S1000 machining centre, in which one side of the workpieces is machined in four-part clamping. The aim was to convert the existing clamping fixture, into which the components were previously inserted manually, to automatic loading with as few modifications as possible. The total machining time including workpiece change was six minutes for four parts, which was also the cycle time determining requirement for automation. A lateral loading door on the machine was modified and integrated into the safety circuit of the machine, as well as that of the robot cell.
A decisive role in the selection of a suitable robot was played by the range required. In order to reach all positions on the fixture, the robot must be able to delve relatively deep into the machine. After carefully considering the necessary precision for handling and inserting the parts, combined with high traversing speed, the company opted for a MOTOMAN GP25 industrial robot with a YRC1000 controller. Numerous installations by EGS in this field of application have demonstrated that Yaskawa robots function reliably in machine tools under adverse conditions over periods of many years.
The second key requirement was the autonomy of the automation system. If possible, the system should be able to operate independently for 12 production hours. For this purpose, a storage capacity for 480 raw parts and 480 finished parts must be available. The dimensions of the geometrically complex workpiece are approximately 145 x 135 x 50mm with a weight of about 200 grams. The SUMO Ecoplex2 from EGS was used for this voluminous stocking of parts. The latter is a palletizing system for workpiece carriers up to a size of 600 x 400mm. The workpiece carriers are stacked, offered to the robot in depalletized form for parts removal and re-palletized after filling with finished parts. In the special design used, with feeding and discharging belts, there is capacity for six workpiece carrier stacks for raw and finished parts. This broad autonomy is made possible by a special reinforced belt design.
Standard, automation-compatible and stackable plastic boxes were selected as workpiece carriers. The workpiece-specific inlays, into which the components are deposited in exactly the required position, were designed by EGS and manufactured by Schwab within its own manufacturing capacities. The right design of workpiece carriers is a fundamental prerequisite for the reliability of the subsequent automation and belongs in the responsibility of a specialist.
A similarly important core component is the gripper technology. Gripper modules of the Zimmer Group as a longstanding supplier are used here. These have proved their worth in numerous implemented applications in the automation of machine tools even under the most adverse conditions. The many years of experience of EGS come to the fore in the engineering and manufacture of the gripper finger itself, as well as the geometrically optimized positioning of the gripper modules on the robot hand in terms of precision, secure hold and optimum accessibility in all gripper positions.
The second face of the workpieces is milled in a second machine, a Brother Speedio S700. Here again, automatic loading takes place laterally through a specially designed loading door. The machining of the second side is far less complex, significantly shorter and done individually. Because the first machine determines the system cycle, the four machined workpieces must be removed directly after machining has been completed, and four new raw parts inserted. A combined deposit and turning station with four workpiece holders serves as an intermediate deposit for the semi-finished parts. Here, the robot drops the components and picks them up again after turning for loading the second machine. After machining and prior to removal, in both machines the components are largely freed of cooling lubricant by means of a blow nozzle mounted on the robot tool, in order to avoid unnecessary contamination.
After machining, a data matrix code must be applied to each component by a coding laser from Koenig & Bauer Coding. As a system manufacturer, EGS Automatisierungstechnik is bound to adhere to laser safety requirements. This is implemented by the appropriate safety guard on the gripper tool and sensor technology that reliably ensures that the laser can only work when the protective barrier covers the full marking area. During inscription the workpiece is securely held in position by the robot, and the resulting fumes are extracted. The applied code contains information on the date of manufacture and a serial number. After coding, the robot replaces the finished part in a workpiece carrier that is placed in the SUMO Ecoplex2 palletizing system on a stack of finished parts and can be removed by the operating personnel depending on availability. The workpiece carrier stacks of raw and finished parts are deposited and removed on one operating side of the system. These can also be prepared at another point and ergonomically pushed onto the belt by a special trolley. Essentially, the system can run unattended for up to 12 hours; existing finished parts can also be removed at any time or new raw parts inserted.
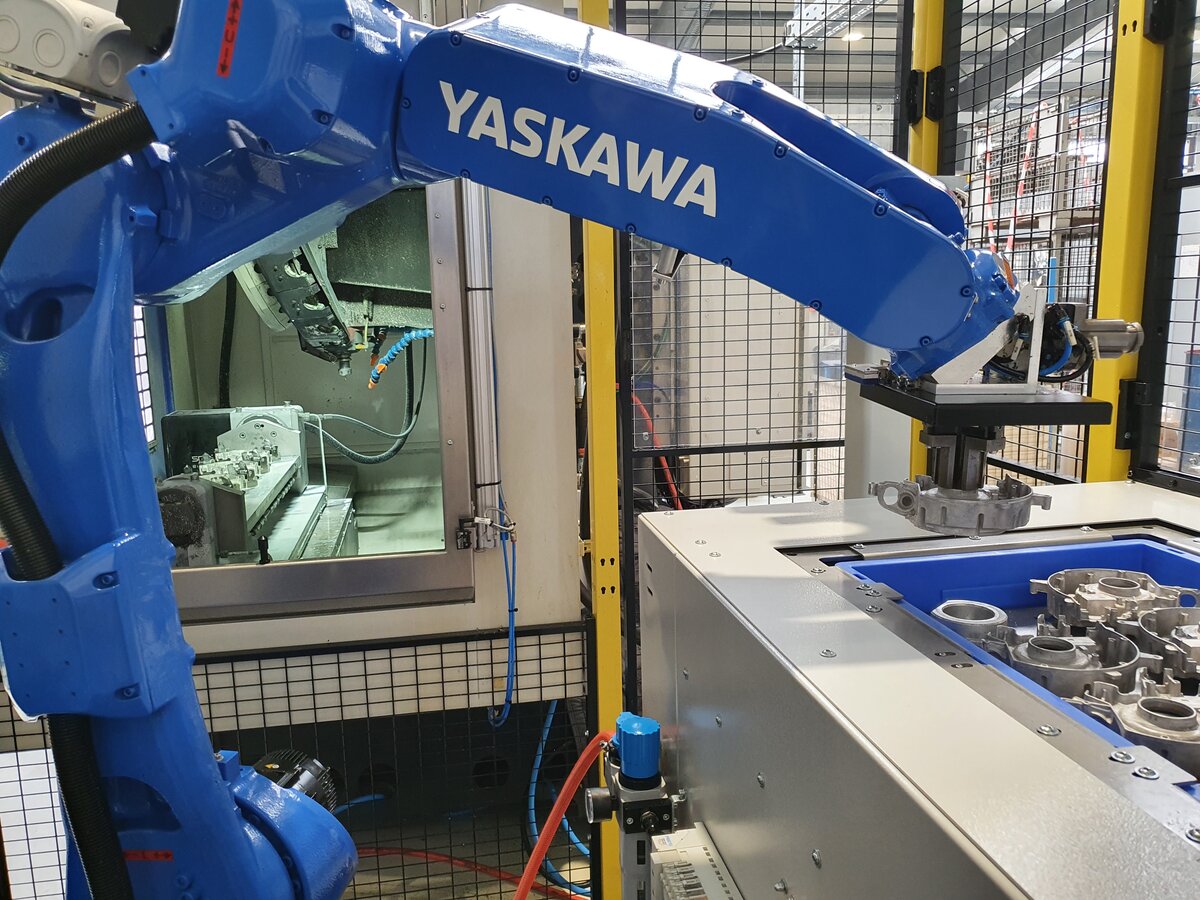
All processes are regulated by the YRC1000 robot controller and the entire system is operated using the lightweight, ergonomic hand-held controller of the robot via a special interface. Following fast and unbureaucratic consultations between EGS and the machine manufacturer, the electrical interfaces to the two machines were implemented on the basis of Profinet. The operating personnel was instructed in the handling of the system in a two-day training course. Although the staff at Schwab CNC Metallbearbeitung had no previous experience with robotics, with these prerequisites they were easily able to operate the system and move the robot manually.
Indeed, the system cycle time was slightly less than that specified, and the robot is faster than the cycle-time-determining first machine.
For Junior Chef Markus Schwab, the bottom line was positive in all respects: “We thank EGS for the trouble-free installation and extremely fast start-up of the system. Due to the SUMO Ecoplex2 we are now able to prevail in the marketplace in times marked by a shortage of skilled labour and offer our customers the desired reliability and flexibility.”
Pictures: EGS Automatisierungstechnik GmbH
Author und Contact:
EGS Automatisierungstechnik GmbH
Heiko Röhrig, Leiter Vertrieb u. Marketing
Fon +49 771 898 606 27
Contact readers’ enquiries Yaskawa:
Tel. +49-8166-90-0
Fax +49-8166-90-103