Med internationellt ledande teknologi vill vi skapa tillväxt på hemmaplan.
Nytt forskningsprojekt använder MOTOMAN-robot
Intuitive robotics solution suitable for the skilled trades
“The fundamental idea was to determine whether it was possible to implement a robot in the skilled trades without special knowledge of programming,” project manager Thomas Planer explains the goal in the development of “Robonet 4.0”. As part of the Skilled Crafts Digital Research Project the Chamber of Trade for Lower Franconia and the Augsburg Fraunhofer Institute for Casting, Composite and Processing Technology (Fraunhofer IGCV) investigated the use of robot technologies of the future by small and medium-sized businesses in assembly and production. Research was focused on the option of intuitively programming robots without a complicated programming code. The robot was to be operated and controlled by human gestures using AR (augmented reality) glasses.
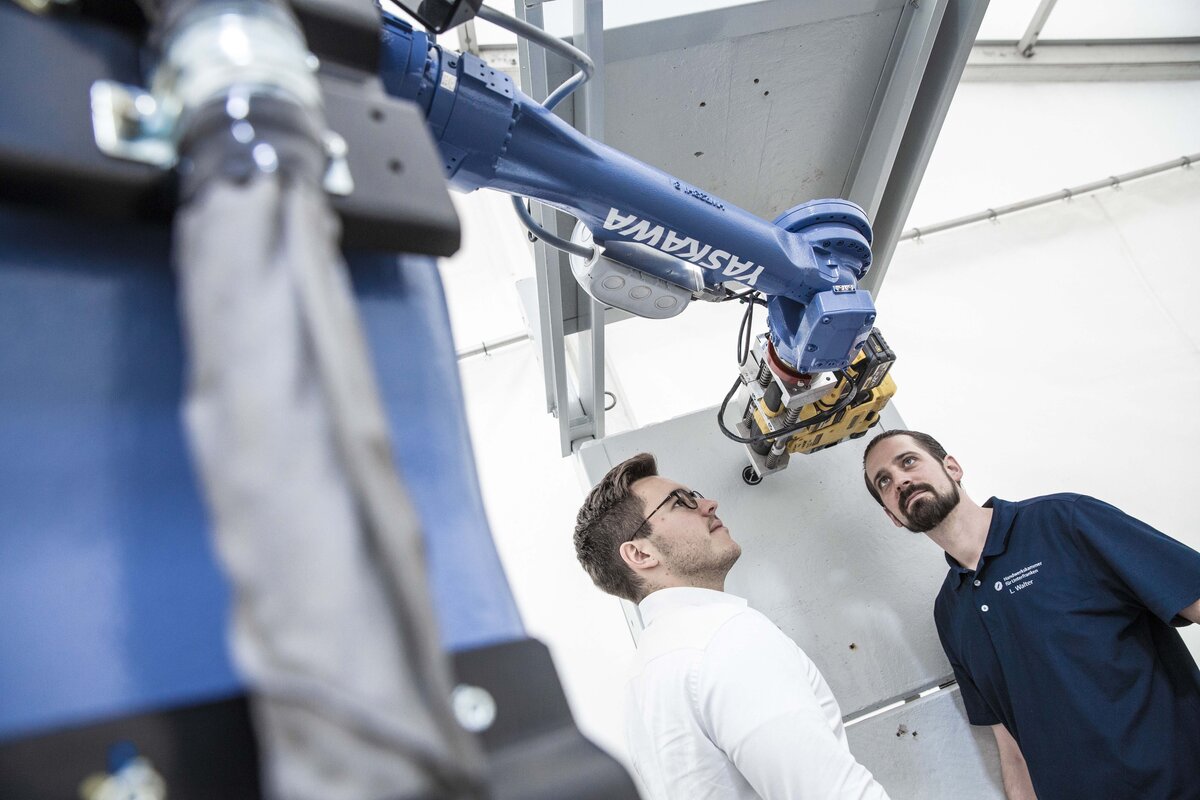
Autonomous drilling with a mobile robot unit
Specifically, a solution for autonomous, robot-based drilling was realized. “We chose this application firstly because the skilled trades have called for machine assistance, particularly for physically demanding work such as overhead drilling in concrete ceilings,” explains project manager Planer. “Secondly, drilling is applicable to many professions and a wide variety of tasks.”
The outcome of the approx. two-year development work is a mobile robot unit. An industrial robot mounted on a moveable platform permits accurate drilling at a height of up to three-and-a-half meters – also above the head. Programming is intuitively controlled using human gestures. In addition, data can be directly transferred from CAD programs.
Flexible MOTOMAN GP
The robot selected for this purpose is a Yaskawa MOTOMAN GP50 with a payload of 50 kg. The decision was made following a public tender. Features that spoke in favor of this model were guaranteed accuracy due to its load-bearing capacity and mechanical rigidity without being too heavy for the mobile base.
The GP series from Yaskawa`s MOTOMAN was conceived for fast joining, packaging and general handling applications. “GP” stands for “general purpose”, i.e. for a variety of uses. Six-axis robots are thus productivity drivers in many industries.
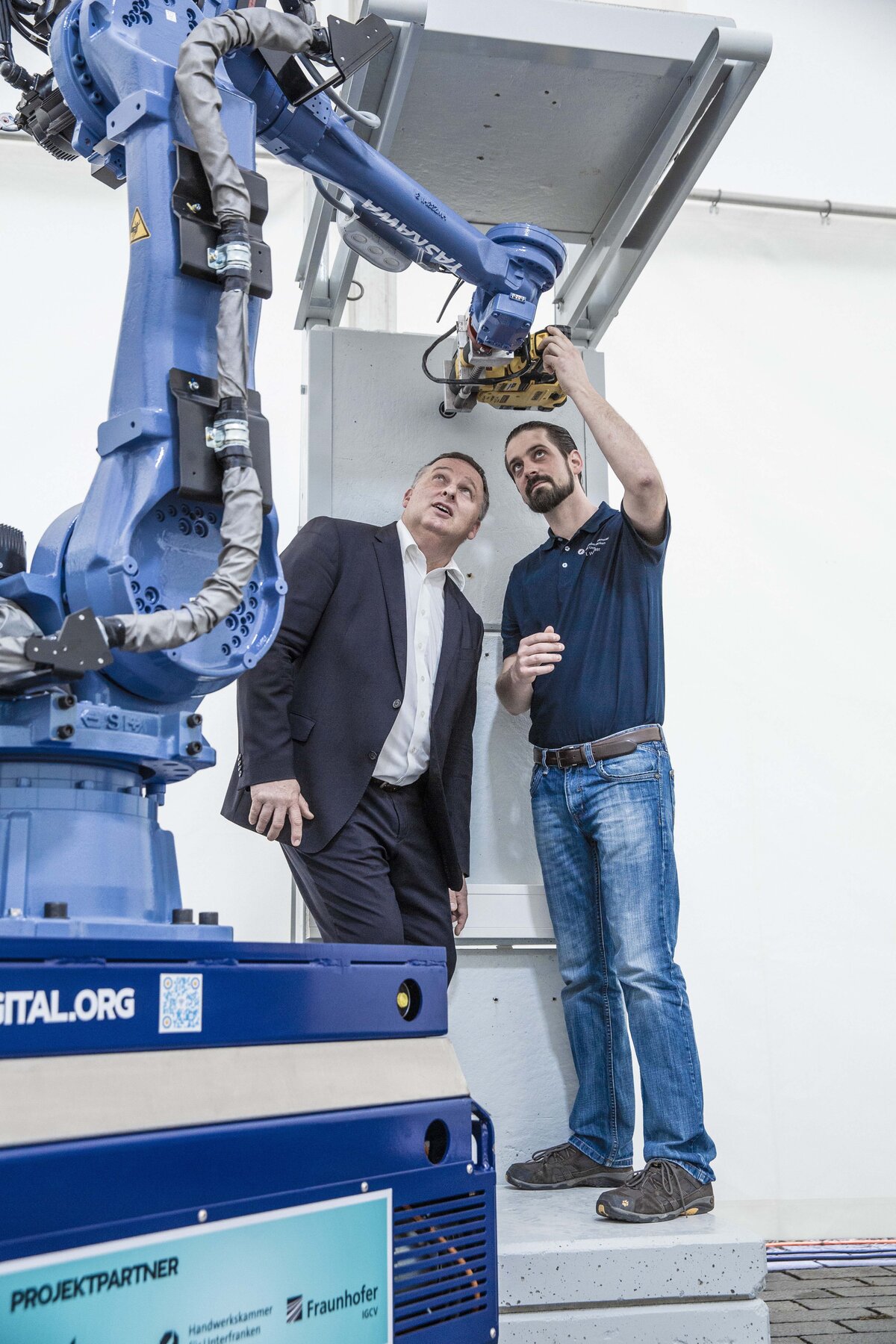
Safety and connectivity
A further argument in favor of the Yaskawa robot was the MOTOMAN YRC 1000 high-performance controller. This exceptionally compact controller with a cabinet volume of only 125 liters permits optimum use of space – and fits into the mobile base of the Robonet 4.0 unit.
An integral safety controller makes the controller a complete Category 3 functional safety unit (FSU) with up to 32 definable safety zones. This enables operation in safe mode and the robot can be safely operated in the specific application without a safety guard.
The hand-held programmer of the YRC1000 controller – the lightest in its category at only 730g – is ergonomically designed and clearly arranged. The touchscreen enables intuitive operation and thus easy movement and scrolling with the cursor. A 3D simulation of the movement of the real robot arm and the limits of the safe working area can be displayed on the screen of the hand-held programmer.
With open interfaces, e.g. to the Ethernet and ROS (robot operating system), the current generation of controllers is predestined for use in Industrie 4.0 environments and for linking to other programs.